3D打印为德国公司节省97%的刀具加工成本和98%的交付周期
- 641
- 0
德国Seuffer公司是一家家用电器和商用机动车零件供应商,主要生产电子机械零件。它是世界上首批将3D打印科技整合融入到它的标准生产流程中的公司之一。因为公司发现,3D打印科技能够显著的减少生产注塑样品零件的时间和成本,从而提高企业的生产效率和获利率。
注塑工艺是全世界在生产零件,尤其是不同材料的零件时最常用的生产工艺。而其最常见的用途则是在规模化大生产之前,为了对设计零件的性能和大小进行测试而用其制作零件原型。注塑工艺的常用原料是热敏塑料。比如说在Seuffer公司就常常需要在运动者的机械环境和高温环境中对汽车零件进行测试。
采用Stratasys公司的3D打印技术之后,Seuffer在几天内就设计好了第一批注塑模具,并在24小时内将它们3D打印完成,然后就可以进行零件测试了。Seuffer公司研发主管Andreas Buchholz说:“以前需要8周时间来用传统的CNC工艺生产金属注塑工具。 而且传统工艺的花费通常在40,000欧元左右,然而3D打印的工具花费则少于1000欧元,也就是说能节省97%。”
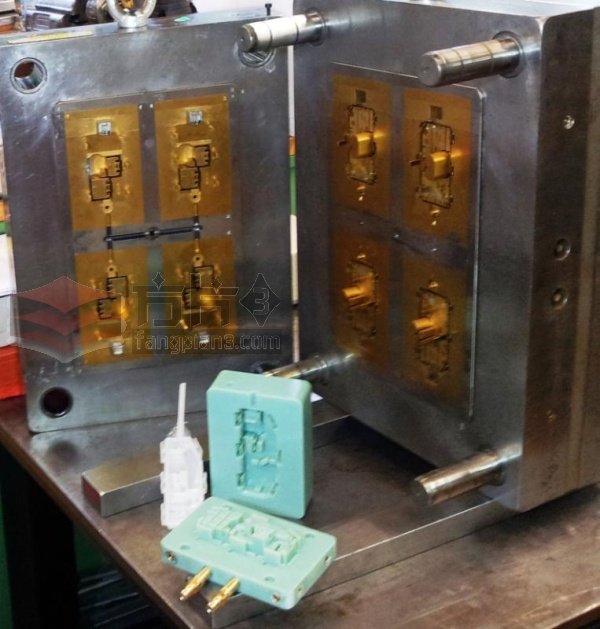
Seuffer公司还用3D打印技术生产热熔工艺所需的模具。这些用于制作电子电路板所需的低熔点聚酰胺外模都是由Stratasys公司推出的坚硬、不透明的Vero材料制作的。
Stratasys公司的总经理Andy Middleton说:“全世界的公司都在为推出他们的新产品寻求能显著提高生产效率的方法,因而都发现了增材制造,也叫3D打印科技的很多益处,” “越来越多的生产商都将采用3D打印的工具作为注塑工艺的补充--不仅仅是在量产之前为测试产品节省成本,同时也会用于生产定制化的零件。”
(新闻源:Marketwatch)
(本文作者为"fangpian3",最初发表于fangpian3.com,该网站现与诺研3D打印服务网合并为同一网站)
注塑工艺是全世界在生产零件,尤其是不同材料的零件时最常用的生产工艺。而其最常见的用途则是在规模化大生产之前,为了对设计零件的性能和大小进行测试而用其制作零件原型。注塑工艺的常用原料是热敏塑料。比如说在Seuffer公司就常常需要在运动者的机械环境和高温环境中对汽车零件进行测试。
采用Stratasys公司的3D打印技术之后,Seuffer在几天内就设计好了第一批注塑模具,并在24小时内将它们3D打印完成,然后就可以进行零件测试了。Seuffer公司研发主管Andreas Buchholz说:“以前需要8周时间来用传统的CNC工艺生产金属注塑工具。 而且传统工艺的花费通常在40,000欧元左右,然而3D打印的工具花费则少于1000欧元,也就是说能节省97%。”
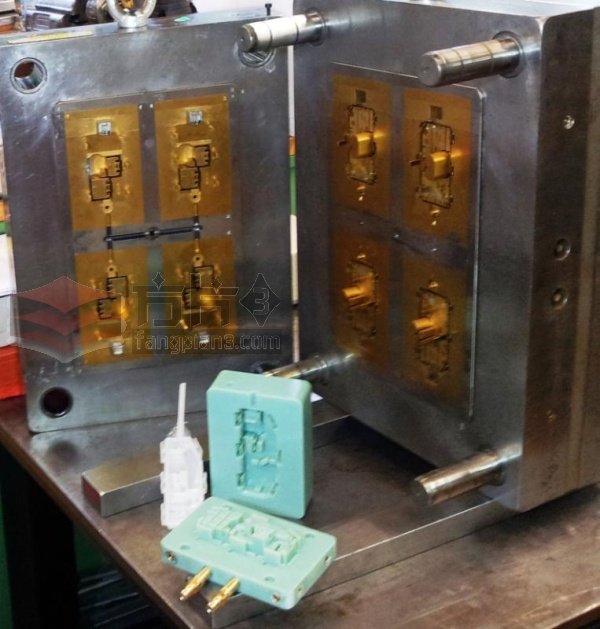
用3D打印工艺以及用传统CNC铣制工艺生产的工具(并排)
Seuffer公司还用3D打印技术生产热熔工艺所需的模具。这些用于制作电子电路板所需的低熔点聚酰胺外模都是由Stratasys公司推出的坚硬、不透明的Vero材料制作的。
Stratasys公司的总经理Andy Middleton说:“全世界的公司都在为推出他们的新产品寻求能显著提高生产效率的方法,因而都发现了增材制造,也叫3D打印科技的很多益处,” “越来越多的生产商都将采用3D打印的工具作为注塑工艺的补充--不仅仅是在量产之前为测试产品节省成本,同时也会用于生产定制化的零件。”
(新闻源:Marketwatch)
(本文作者为"fangpian3",最初发表于fangpian3.com,该网站现与诺研3D打印服务网合并为同一网站)